Hello TUBA blog readers and welcome!
My name is Hrafnhildur Helga, but I am known as Helga outside of my home in Iceland. I have been a PhD student at Teesside University in Northeast England for just around three months now and as such form one part of the TUBA team. My research is still in its early stages, but focuses on the leather shoes and burial environment of Roman Vindolanda. For more information on me, please check out the ‘meet the team‘ section of this website.
As part of my research, I am excited to introduce my first blog post of (hopefully) many, about a research trip I took last week to learn about leather manufacturing first hand.
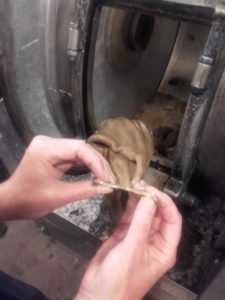
When it comes to interpreting data on archaeological leather and leather making – which is something I will be doing throughout the course of my PhD – nothing beats knowing a little bit about how to actually go about it. So, last week I attended an amazing course at Northampton University, called ‘Understanding Leather – From Tannery to Collection’, hosted by the Leather Conservation Centre and the Institute of Creative Leather Technologies. The course was held and attended by researchers and conservators knowledgeable on the process by which vertebrate skins can be converted into leather. Course teachers include Yvette Fletcher, an experienced historic leather conservator, Anne Lama, a leather chemist, and Dave Sherwood, the tannery manager, who has been worked in or around tanneries since age nine. If the last name does not ring a bell, he is perhaps most famous for having – during the course of this same week – led ‘team Dave’ to victory in a tournament of bar-Skittles against ‘team Yvette’, a feat this member of team Dave is very proud of.
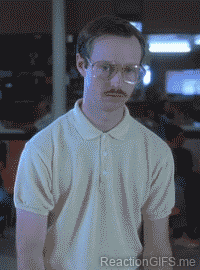
Besides being plain fun – having attended this course will be incredibly useful when it comes to interpreting any data acquired in my PhD project, which focuses on the leather shoes from Vindolanda. The tanning process was followed through from fleshing to finishing, and any questions and requests were met with flexibility and enthusiasm. By the end of the course, I had not only learnt about tanning leather, but been introduced to a multitude of scientific tests and methods to identify different species, tanning qualities and traditional methods at different localities. Getting to know and hear about the leather research being carried out by the course attendees was absolutely great too, as it broadened my horizons regarding how many questions remain unanswered when it comes to leather making in the past.
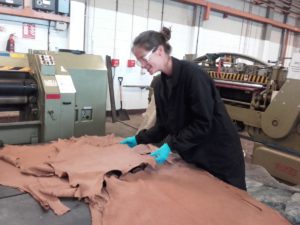
The attendees of the course this year were a mixture of archaeologists and conservators, but the course can be useful to anyone interested in leather making, old and new. The group this year was absolutely great, with an all-female cast. I generally find that am continuously amazed at the wealth of excellent and enthusiastic people and researchers around the world, and the people I met this week were no exception to that trend.
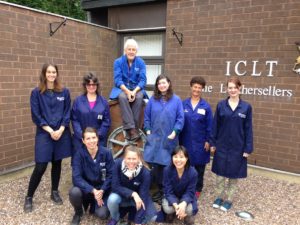
During the week, each student got to tan, oil and decorate their own animal hide, following the process through from start to finish, and to top things off we got to take our resulting leather home! The Institute of creative leather technologies has amazing facilities for applying creative and innovative processes and decoration options to leather, which is what most students involved with modern leather making are interested in. However, as most of us who attended this course this time deal with artefacts from the past, we were overall more interested in viewing our leather as a window to the past and as sample material, using simple methods for tanning, oiling and decorating. For myself and this project, I was most interested in vegetable oak bark tanning, commonly associated with Romans, contemplating the ways in which decision-making in the tanning process could influence the resulting strength of leather, and eventually its resistance or reaction to the archaeological burial environment at Vindolanda. As such, it is truly invaluable to have been given the opportunity to experience the process first-hand, especially this early on in my project.
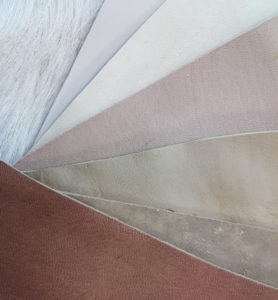
Despite our general reluctance to apply modern techniques to our leather, we did get to put our artistic skills to the test – as the team at Northampton were quick to accommodate our reluctance in treating our precious sample material, and let us experiment with leftover material from previous batches. Which was great fun! Although I am very thankful that I got to try out these different methods and put my artistic skills to the test with various dyes and oils, I must say I found my artistic skills somewhat underwhelming. So, before ending this post, I will give you a glimpse of my proudest artistic attempt from the week – in the form of a TUBA tribute that took much longer to make than I would like to admit:
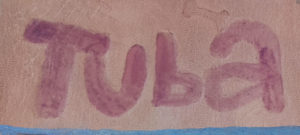
Thanks for reading!
Helga